sqe課程的問題,我們搜遍了碩博士論文和台灣出版的書籍,推薦馬曉峰寫的 避開采購黑洞 可以從中找到所需的評價。
另外網站【數位同步學習課程】VDA6.3 製程稽核實務實戰也說明:課程 講師蘇峰民博士為國際認可之ISO 9001:2015主導稽核員、VDA6.3 2016年版過程稽核& VDA6.5產品稽核員、六標準差 ... 供應商品質稽核人員:採購,SQE,工程技術人員;.
國立臺灣科技大學 資訊管理系 李國光所指導 金蘭剛的 ODM/OEM產業協同研發典範建立之探討 (2015),提出sqe課程關鍵因素是什麼,來自於代工設計、風險管理、協同研發設計、同步工程、品質管理、典範學習。
最後網站SQE专题,学习SQE的课程资料-SQE培训 - 森涛培训网則補充:SQE 培训课程专题,内容包含SQE相关学习资料:SQE培训SQE文章SQESQE课程及SQE下载等. ... 课程对象:高层管理者、采购部门、品管部门、设计部门、财务部门及其他相关 ...
避開采購黑洞
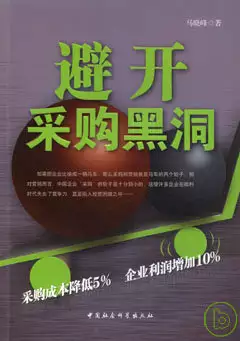
為了解決sqe課程 的問題,作者馬曉峰 這樣論述:
如果把企業比喻成一輛馬車,那麼采購和營銷就是馬車的兩個輪子。相對營銷而言,中國企業“采購”的輪子是十分弱小的,這使許多企業在微利時代失去了競爭力,直至陷入經營困境之中…… 采購部門是一個“賺錢”的部門! “采購額下降5%,企業就可以增加10%的利潤!” “采購的專業化管理被企業當成‘利潤中心’來經營,因為它是企業核心能力之一!” “在BONEIMEN公司,如果采購額下降2%,可以提升3.7%的利潤!” 現代工商企業經營管理之道是通過制成品來換取合理的利潤。但原材料價格不斷地上漲及客戶的要求不斷地改變,諸如,產品品種變化大、批量小、交貨期短、質量
高、價錢低等,都使得企業要達到這個基本原則變得越來越困難。企業要想維持競爭及保有合理的利潤,就只有紛紛發揮采購的功能及專長。爭取以最低的成本,適時地取得品質優良的合適材料或設備,以確保企業順利運轉並獲取微利時代的生存利潤。對制造業來說,采購成本佔了生產總成本的55%~85%,若采購成本能降低5%~10%,則產品利潤可直接提升5%~10%。由此可見,采購在企業內具有不可或缺的重要地位。但是,采購的主要功能還必須要和銷售市場的推廣、研發、生產計劃、物料計劃、生產能力計劃、質量控制、存貨控制、庫存管理等環節互相協調及配合,才能獲得合理的投資回報率。 基于采購管理在企業中的重要影響力,本書編
者憑借多年的采購經驗,揭示了在采購管理中,降低成本、議價技巧、供貨商管理、供貨商交貨期管理、采購流程、品質管理等方面的內容,令讀者實實在在地掌握並學會運用采購的技能和技巧。 馬曉峰,復旦大學管理學博士。德國漢堡大學工學博士、美國華盛頓大學訪問學者、美國采購協會會員。曾任中國第三方物流網CEO,司達物流信息系統管理(中國)公司總經理,復旦大學國際經營技術講習所副教授,上海勞動局職業指導中心顧問,上海緊缺人才辦公室指定顧問等。他主講的課程有︰“采購、庫存戰略管理和控制”、“物流與供應鏈管理、物料控制”、“渠道管理、物流成本控制物流的客戶服務”、“倉庫的流程性管理”、“運輸配送的戰略控制
與管理”,“信息技術在物流運營中的管理”等。 序一 序二 前言 第一章 采購管理的新型理念 第一節 供應鏈管理體系下的現代采購模式探索 第二節 物流的沖擊對采購的影響 第二章 現代企業的主要采購方式 第一節 電子化采購 第二節 JIT采購是什麼 第三節 外包采購 第四節 不要把招投標采購做成“陽光下的交易” 第五節 集中采購與分散采購 第三章 采購的核心與采購流程優化 第一節 采購的核心︰服務 第二節 采購部門人員的組織 第三節 采購部門與生產、物流、財務、銷售等部門的交叉關系 第四節 采購流程的管理和
控制 第四章 供應商的選擇 第一節 如何依據公司發展目標制定選擇體系 第二節 供應商的開發、考察與信息管理 第三節 篩選供應商應考慮的因素 第五章 供應商的精細化管理 第一節 交貨期管理 第二節 品質管理 第三節 供應商的服務及其他管理 第四節 供應商的關系管理 第五節 供應商的考核機制與改善供應商績效, 第六章 采購成本分析與控制 第一節 “采”、“購”分開與降低采購成本 第二節 采購成本的結構與降低采購成本 第三節 供應商庫存管理系統VMI與降低采購成本 第四節 其他采購管理策略與降低采購成本 第五節 綜合
采購方法推薦 第七章 采購談判與合同管理 第一節 SWOT定位分析 第二節 談判前的準備 第三節 談判中的技巧 第四節 談判後的結束 第五節 談判綜合技巧瀏覽 第六節 合同管理 第七節 合同範本借鑒 坦白地講,出書這件事已經是我很早以前的想法了。到現在已經差不多2年了。之所以耽誤了,是因為我的工作比較忙,實在沒時間。我曾經盤點過2006年的所有出差用的登機牌,共有98張,也就是平均一周出差2次,所以根本沒時間坐下來寫東西。供應鏈的工作本來就很痛苦,有很多是突發的、臨時性的事情,常常會弄得你措手不及,直至把你搞得焦頭爛額為止
。2007年,我的工作理順了許多,這才有時間著手整理這本書稿。不過,直到現在我才明白,別的人都是在享受生活,而我,生活是在享受我。 采購是什麼,我有時候自己都說不清楚。但是采購確實充滿了不確定性,充滿了懸疑,充滿了挑戰。我記得最忙的時候是2006年4月份,那時候,供應商交貨期的準時率為47.5%,資金周轉超快,庫存居高不下,計劃準確率幾乎為零。老板當時還火上澆油,他居然想把大部分供應商的應付款周期拉長到120天,我雖然表示了不同意,但考慮到他和公司的處境,只有勉強答應了。那段時間我幾乎天天做噩夢,有時候連做夢都是上下集的,中間起來上個洗手間,回來再接著做夢,內容居然都能連起來。每當我
白天坐在辦公室里,就覺得自己仿佛是坐在一個幽深的洞里,里面黑的伸手不見五指,我在里面歇斯底里地喊,累得筋疲力盡,癱倒在地,但是卻能清晰地听到洞外人們說話的聲音,可是他們沒有一個人來搭救我。那些聲音來自不同的部門和不同的人,有生產部門的、有銷售部門的、有財務部門的、有計劃部門的…… 在夢里我就發誓,將來一定要把這些聲音記錄下來,如今如願了。在這本書里,我描述了采購部門和采購業務應具備的框架和功能體系.它也是我能記錄那些聲音的有力工具。 [畫外音] 2006年4月9日,江蘇徐州的一個供應商給出了他的報價清單,其中有三項要漲價,分別是人工費、鋼材和不銹鋼,有三項保持不變
,分別是包材、橡膠、樹脂。可是,就在2天前,我和這個供應商的銷售總監還一起在北京中石化開過會.我明明看到中石化的橡膠和樹脂基料便宜了5%的。于是.我打電話問他,他很尷尬地說︰“抱歉,我忘記了。”真是狡猾,這不是黑洞是什麼? 2006年7月初的某天,在上海菜福士廣場一樓的星巴克咖啡館內,老板跟我說︰“馬,你知道我們銷售部門的應收賬款的周期嗎?”我說︰“知道,大概在22~40天。”老板說︰“馬,我希望你們采購部門的應付賬款的周期應該在120天。”我當時感到一陣頭暈,心想,上帝呀,他認為現在的這些供應商都是傻子嗎?這讓我以後怎麼做?這不是黑洞是什麼? 2006年10月的某天,在蘇
州工廠的會議室里,一個銷售工程師怒氣沖沖地對著我的采購工程師大聲喊道︰“怎麼了.我就是要今天下訂單,明天要貨,不給你們壓力是不行的,還反了你們了,別忘記了,你們的工資是誰賺出來的。”我的采購工程師一臉無奈,臉部肌肉不停地抽搐著,最後氣得癱在椅子上。目光呆滯。這不是黑洞是什麼? 2007年5月11日,由于供應商的高層更換頻繁,導致交貨期嚴重滯後,我的2個Buyer和2個SQE幾乎在廣西柳州的工廠里連續工作了12天,他們回到上海後,卻沒有一個部門對他們表示同情。這不是黑洞是什麼? 2007年6月底,采購部門一個Sourcing買了一款新手機,沒想到,人事部門卻強行介入調查這個
手機是誰送他的,一個月後,調查得出的結論是他正常買來的,我的這個Sourcing因此而辭職,並聲稱要與人事部門對簿公堂,經協調後,事件得到平息,我卻由此損失了一員愛將。但後來人事部門一個經理的話卻讓我氣憤不已︰“誰讓他是采購部門的,那個手機很貴的,他的工資買得起嗎?”這樣的話也說得出來,這不是黑洞是什麼? 2007年8月,我的采購經理向我抱怨財務部門的流程太呆板︰“因為現在的供應商都很強勢,要先看到我們開出的支票才給開發票,而我們的財務部門卻堅持要先看到發票再開支票.為此我總共跑了4趟進行協商,以後再也不想跑了。”這不是黑洞是什麼? 采購部門經常處在公司、企業的風口浪尖
,做好了是生產和銷售的功勞,做不好就是采購的責任。 無論是誰,都可以隨時隨地投訴采購人員。 花錢誰不會花呀?是人都會做采購。 不希望這樣的事情也在讀者的公司中出現.屏蔽采購的黑洞,做好供應,這才是我的初衷。
ODM/OEM產業協同研發典範建立之探討
為了解決sqe課程 的問題,作者金蘭剛 這樣論述:
台灣的科技代工業萌芽於1970年代,隨著國際品牌大廠的不斷成長,帶動了台灣製造業的經濟起飛以及代工業(OEM, Original Equipment Manufacturer )成長。在產業分工越來越細之下,製造商也各自發展出屬於每個企業所特有的專長與能力。因此,比起早期的代工業,以代工設計製造業(ODM, Original Design Manufacturer)更能夠協助客戶進行產品設計發展及製造模式也逐漸發展起來。在競爭激烈的全球化產業發展下,滿足客戶對高效率、高品質、低成本的需求是企業最重要也是最關鍵的競爭優勢所在。「變形金剛」、「電競筆電」、「平板電腦」,或是輕、薄、短、小或是以產
品效能為主,這些皆是後PC時代下產品商業發展的特色。同時全球筆記型電腦品牌客戶競爭激烈,市占率互有消長,更是為了保有競爭優勢所需,對創新、品質、交期、成本的目標驅動下,與代工設計及製造廠商合作則至關重要。CoClever公司面對品牌客戶外在壓力與組織內部問題錯綜複雜下,在研發設計團隊中,從觀念建立,思維改變,淺移默化的將同步工程的協同研發模式,依序地深植於組織團隊裡。借助於新產品開發導入「產品風險管理計畫」,除了產品研發單位(RD),同時也邀集生產製程設計單位(PE),供應商品質工程單位(SQE),設計品保單位(DQA) ,共同合作,同心協力,以卓越品質設計為共同目標,從而來闡述協同研發之同步
工程的重要性。對於ODM代工產業長期3%至4%「毛三到四」的低毛利壓力下,如何快速設計並且發展合乎客戶品質期望的成本優勢產品,個案在推動過程中,透過生產廠區在跨團隊的典範學習模式下建立出一標準化新產品開發流程的設計驗證管理平台,為所有筆記型電腦相關供應鏈產品研發所用。未來更進一步,能將此典範模式快速複製於集團下其他的產品線上,維持企業的競爭力,提升企業的價值。本研究相關理論為組織學習理論中對於建構學習型組織的重要,協同研發設計管理對設計開發階段到量產階段的高品質、高生產良率間的關聯性,最後是典範學習與複製理論等。本研究另可應用於大型科技製造業之產品研發中心與全球化海外製造中心的組織運作下,如何
學習與發展出一優質化的協同研發設計的新產品資料管理平台。
sqe課程的網路口碑排行榜
-
#1.供應商品質管理工程師(SQE)崗位職責與能力模型淺析 - 人人焦點
SGS管理學院在供應鏈管理方面有著非常豐富的經驗,擁有多名供應鏈管理方面的專家與資深講師,除了專門針對以上提到的SQE課程,還提供供應商質量管理、供應商選擇與評估 ... 於 ppfocus.com -
#2.SQE供应商质量管理与工具运用 - 豆丁社区
为此我们结合多家知名跨国公司的运作管理模式,结合本身咨询师的工作经验以及最新的物料品质和供应链管理知识,专门开发了这一个面向制造业SQE的专项课程。 於 m.docin.com -
#3.【數位同步學習課程】VDA6.3 製程稽核實務實戰
課程 講師蘇峰民博士為國際認可之ISO 9001:2015主導稽核員、VDA6.3 2016年版過程稽核& VDA6.5產品稽核員、六標準差 ... 供應商品質稽核人員:採購,SQE,工程技術人員;. 於 college.itri.org.tw -
#4.SQE专题,学习SQE的课程资料-SQE培训 - 森涛培训网
SQE 培训课程专题,内容包含SQE相关学习资料:SQE培训SQE文章SQESQE课程及SQE下载等. ... 课程对象:高层管理者、采购部门、品管部门、设计部门、财务部门及其他相关 ... 於 www.stpxw.com -
#5.SQE供应商质量管理培训课程 - 天天直播nba百事通
SQE 供应商天天直播nba百事通管理培训课程. 企业竞争不能靠单打独斗,需要同供应商形成战略合作伙伴关系,如同日本丰田的成功离 ... 於 tdjzfz.com -
#6.供應商管理(資深)工程師(SQE) - 1111人力銀行
食品安全管理系統主導稽核員訓練課程 ... –課程的完成,學員應能: –說明FSMS 的基本目的,以及食品安全危害的評核與管理。 –說明FSSC 22000 and ISO22000 相關指引文件的 ... 於 www.1111.com.tw -
#7.SQE-供应商质量管理高级研修班 - 华阳企管
课程 背景: 企业间竞争已成为整个供应链的竞争是不争的现实,企业生存的内外部环境 ... 於 www.huayangqiguan.com -
#8.英國專業文憑課程-法律 - 睿智國際教育顧問有限公司
行之有年的法律轉制課程(Law Conversion Course)-GDL被視為最佳的考試準備 ... 可以是遵循舊有的模式完成律師訓練,也可以選擇直接加入SQE的律師考試 於 wisdomiec.com -
#9.显示全部4 个法理学文学硕士学位在线课程文学硕士项目
University of Law SQE. 伦敦, 英国. 我们的新硕士法(SQE1)是法律转换课程,其中包括我们的SQE1预备课程,该课程为学生进行SQE1评估做准备。该课程是为希望获得律师 ... 於 www.onlinestudies.cn -
#10.SQE供应商质量管理及工具运用 - 六西格玛品质网
课程 背景: 近年来我们听到越来越多的因产品质量缺陷所引起的事故。随着信息传递速度的加快,被置于公共视野的企业很可能因为一次质量事故而受轰然倒塌。 於 www.6sq.net -
#11.【经验分享】 | SQE的核心工作是消除7大浪费—— 行业资讯
【工具讲解】| 别让FMEA这只“飞马”真的飞啦! 关于我们|热门课程|诚聘英才|奥 ... 於 omnex.com.cn -
#12.教育學術組標準作業要點 - 長庚醫院
每月一、 配合教學組訂立之年度計畫,安排組員負責協助課程業務。 二、 協助課後評值,以激發人員對課程之參與度。 ... 五、 人員SQE(資格與教育)存檔。 於 cghdpt.cgmh.org.tw -
#13.SQE的培训课程有哪些? - 百度知道
3 供应商质量开发,协助供应商对产品和制程进行质量改善。 4.供应商绩效评定以及质量改善推动: A.每月对供应商的入料,上线品质状况,报告回复的时效和配合 ... 於 zhidao.baidu.com -
#14.SQE Law Essentials在线-全日制, 香港, 香港2021/2022
通过我们新的SQE 法律要点课程开始您的法律之旅,这是计划升读SQE1 的非法律专业毕业生的第一步。这个简短的在线课程将向您介绍SQE1 所需的法律知识要点。 於 www.lawstudies.cn -
#15.#新sqe制度下的新課程 - Jelajah | Facebook
英國法律實務課程(LPC)與香港法律學深造證書(PCLL)一樣是畢業生在現行制度下必經的專業進修課程… Lihat Lagi. 【講座】如何在英國及香港成為律師? 於 ms-my.facebook.com -
#16.委外管理第二版 - 第 i 頁 - Google 圖書結果
... 接著大型台商又發現雖有組織機能,但責任執行者素質明顯落差大,因此筆者曾被客戶要求提供「委外技術者之專業課程」,因而規劃「供應商品質工程(SQE)」,把筆者和過去 ... 於 books.google.com.tw -
#17.供应商质量工程师(SQE)是做什么的? | 优思学院
优思学院有限公司(UCOURSE Limited),致力于为在职人士建立云端网上课程、考试认证,促进人才培育,个人发展,和技能提升。加入我们的微信公众号,可以 ... 於 ucourse.org -
#18.CQPE®學長心得 - 科建顧問
自己工作是FAE、PQE、SQE工作內容,很多客戶會要求SPC,在近2個月在公司QIT小組有推行X-bar R Chart部分,透過課程的學習表單公式設計符合公司SPC管制,以及製作自己工作上 ... 於 www.kind.com.tw -
#19.【講座】如何在英國、香港兩地成為律師?英國法律系碩士階段 ...
英國法律系碩士階段課程簡介會(The University of Law) 英國新事務律師專業考試(SQE)對學生有何影響? 類別網上升學講座. 對象 ... 於 www.britishunited.net -
#20.2月24日(三) 下午7時至8時英國The University of Law 法律學 ...
當中將重點講解四大課程,包括法律深造課程Postgraduate Diploma in Law (PGDL) 、法律實務碩士課程LLM Legal Practice、SQE 考試預備課程SQE Preparation Course 及大 ... 於 aston.edu.hk -
#21.SQE供应商质量管理培训课程
这些工作一般由专门的职位--SQE(供应商质量管理工程师)来完成。本课程就是专门针对注册认证SQE而开设的。课程以务实操作的七大主题内容指导SQE如何更好地开发、 ... 於 bjylgj.org -
#22.SQE供应商质量管理及工具运用评论列表-培训课程-总裁班团课网
首页 · 培训课程 · 团课活动 · 培训机构 · 开课通知 · 资讯头条 · 微视频 · 院校图库 · 培训讲师. 发表评论首页 > 培训课程 > SQE供应商质量管理及工具运用 > 评论列表 ... 於 tuanke.org -
#23.Law Conversion Course (PGDL) - PG Diploma at BPP University
了解更多有关BPP University Law Conversion Course (PGDL)的课程内容,奖学金信息,申请条件和入学成功率评估的更多信息,然后开始出国留学! 於 sara.intake.education -
#24.SQE供应商质量管理课程
【课程目标】: 1、透过2天的培训,对于有品质基础并有一定管理能力的管理人员或工程师可以担当SQE 2、帮助企业建立,训练和优化供应商管理团队,重点培养SQE 3、掌握从 ... 於 www.zongceiso.com -
#25.SQE供应商质量管理
SQE 供应商质量管理高级研修班. 课程收益. 1. 掌握最新的供应商质量管理系统构成. 2.理清供应商质量管理的系统路径,消除头绪繁杂的困惑,最终实现高度简洁化和计划性. 於 jsqasoft.com -
#26.科建管理顧問股份有限公司-公開課程
課程 名稱, 班組長必須要學會的品管實務技巧, 課程時數, 6. 上課地點, 請見下方場次資訊 ... 台灣捷康綜合有限公司(IC 封裝測試產業)IQC/SQE/IPQC品保高級工程師2. 於 vip.asia-learning.com -
#27.計劃移英後投身法律專業The University of Law 多元進修課程導覽
完成兩個階段的SQE 評核後,申請者需要進行為期兩年的法律工作經驗(Qualifying Work Experience – QWE)。但相比傳統「LPC 模式」下的Training Contract ... 於 www.thestandnews.com -
#28.SQM供應商管理與輔導- 進修課程
本課程將教導您如何在供應商管理上,以最有效之管理及輔導方法來協助供應商, ... 供應商管理之重要性*公司規模與供應商類型*供應商輔導-SQE輔導能力培養-日常 ... 於 www.1111edu.com.tw -
#29.營業員資格考試SQE 課程(細牌)(S牌)第4部分[不是Past Paper ...
本影片不是Past Paper, 不是Pass Paper, 不能Download, 不能下載,沒有PDF主要講述營業員資格考試SQE (細牌)(S牌)課程第1部分內容,如同學如需購買模擬試題進行練習, ... 於 yt.d0.cx -
#30.SQM供應商管理與輔導-公開課程 - 亞太教育訓練網
對本課程有興趣者或製造、品保、採購及進料檢驗等相關人員. 【課程大綱】 一.供應商管理之重要性 二.公司規模與供應商類型 三.供應商輔導 3.1 SQE輔導能力培養 於 www.asia-learning.com -
#31.认证SQE 培训课程 - 无忧文档
提供认证SQE 培训课程word文档在线阅读与免费下载,摘要:认证SQE培训课程1.课程简介:企业间竞争已成为整个供应链的竞争已是不争的现实,面对供应商管理诸多因素中, ... 於 www.51wendang.com -
#32.營業員資格考試SQE 課程(S牌)第3部分[不是Past Paper不是 ...
營業員資格考試SQE 課程(S牌)第3部分[不是Past Paper不是Pass Paper不是試題不是精讀不能Download不能下載].VID084. 」@youtube ↓↓↓的用户也观看了(Often Viewed ... 於 cn.av4.space -
#33.認識SQE: 成為英國事務律師的新不二「法」門
要在英國成為事務律師(Solicitor),目前大部分同學選擇從傳統的法律學士學位開始,也有一些本身不是法律學位出身的同學,透過修讀法學轉制課程(law ... 於 linkedu.hk -
#34.供应链质量管理(SQE) - FMEA培训
课程 费用:3600RMB/人(含培训费、资料费、证书费、税费、午餐及茶点等),3人以上团体报名9.5折优惠,免费赠送MINITAB软件套。可安排进厂内训,受训名额不限。 3.SQE供应商 ... 於 www.fmeapx.com -
#35.華為在台供應鏈管理部隊曝光 - 財訊
SQE 的主要工作職務包括供應商品質稽核、供應商評鑑、進料系統管制、輔導供應商品質。也因此,例如當供應鏈廠商產線、產品、良率等出現重大問題,訊崴 ... 於 www.wealth.com.tw -
#36.SQE-供应商质量管理高级研修班
SQE -供应商质量管理高级研修班企业培训课程是行课网提供质量管理类培训丁老师讲师主讲的课程,SQE-供应商质量管理高级研修班企业培训课程属于质量管理领域企业培训课程 ... 於 www.daosendba.com -
#37.SQE供应商质量管理课程培训 - ISO体系认证咨询
SQE 供应商质量管理课程培训. 更新时间:2020-08-15 10:15:35 来源:卓悦思达. 【ISO9001质量管理体系概述】. ISO9000质量管理体系是企业发展与成长的根本,ISO9000不是指 ... 於 isowh.cn -
#38.无锡SQE管理培训课程-胶东在线考试培训 - 蓝鲸体育ios
无锡SQE管理培训课程. 无锡诺达名师 作者:佚名 2020-12-11 16:43:08. 大家都知道质量是对于制造业来说是基础,那么影响质量的要素有,供应商质量保证,客户质量保证, ... 於 hebeijiayuan.com -
#39.SQE供应商质量管理培训课程-掌握日常的供应商质量管理方法
SQE 供应商质量管理培训课程-掌握日常的供应商质量管理方法. 首页; 前进; 后退. 请先关注公众帐号. 1点击右上角分享按钮查看公众号. 2在【添加朋友】—【查找公众号】中 ... 於 m.vcooline.com -
#40.首頁| 中原大學推廣教育處Office of Continuing Education ...
運動舞蹈 國際語文 創業育成 商管金融 資訊電腦 美味食尚 設計裝修 師資培訓 政府委訓 生活時尚 藝文創作 音樂教室 兒少與成長 營隊課程 樂齡大學 學分專班 隨班附讀 於 oce.cycu.edu.tw -
#41.SGS丨全球公认的质量基准-第三方认证机构-计量检测公司-产品 ...
本课程结合经典案例分享,向学员提供了一种系统而全面的供应商质量管理方法论,从而使供应商质量管理人员更好地做好供应商质量管理工作 ... SQE/SDE 应具备的基本素质. 於 www.sgsonline.com.cn -
#42.英国法学大学专题博客-我应该学习LPC 还是SQE课程? - 知乎
SQE 为学生提供了进入法律职业的全新途径。目前,我们收到诸多学生对于决定SQE 还是LPC 的疑问,因此,我们采访了ULawSQE 课程设计的项目负责人Jill Howell Williams ... 於 zhuanlan.zhihu.com -
#43.SQE-供应商质量管理及工具运用
SQE -供应商质量管理及工具运用课程培训,全面系统的介绍了供应商管理的核心思想与技巧,并提供供应商管理所应用的最新最实用的工具,可提升学员的综合能力,拓展知识面 ... 於 m.annakaryoti.com -
#44.供应商质量工程师SQE-学习视频教程 - 腾讯课堂
如对课程有疑惑及建议,可以发邮件[email protected]给老师,老师帮您答疑解惑,让你轻松掌握课程知识!同时将赠送全套免费课程的PPT哦。 专门为SQE开发的岗位课程, ... 於 ke.qq.com -
#45.上海SQE供应商质量管理及工具运用
开课时间: 2021-11-25; 课程分类: 质量管理; 结束时间: 2021-11-26; 授课老师:; 课时: 12课时; 课程评分:; 开课地点: 上海; 课程价格: ¥4200/人 ... 於 21cniso.com -
#46.SQE:供应商质量管理及工具运用 - 采购
【课程简介】. 物料质量和供应商管理在不同的企业中的应用,使SQE(Supplier Quality Engineering)的职位应运而生。事实上,供应商品质管理的内容非常丰富,涉及质量 ... 於 www.yumaster.com -
#47.2019上半年品質技術師(CQT)證照培訓(高雄班)
課程 說明品質學會的『品質技術師證照』是高居第三最受歡迎之證照,摘錄自經濟日報105年2月11日證照情報,是工程領域的三種證照之一,是品管(品質)或品保工程師入門必修 ... 於 www.csq.org.tw -
#48.2021/10/14] NVIDIA 2022 (111) 研發替代役RDSS Intern 擴大 ...
SQE /Server Factory Planner / NPI Project Manager (IE). · Failure Analysis. 詳閱職缺內容. 搜尋 Taiwan RDSS. 上傳英文履歷。成績單. 於 www.me.ntu.edu.tw -
#49.舌尖上的科學: SM918 - 第 69 頁 - Google 圖書結果
SQE \團*忒作謁 KN「。霄、 - -『-下下。超越學校課程的突破性研究報導,提供與全球科學家同步思考的前瞻性思惟,兼具故事性、知識深度與趨勢觀,是領域分類研究與學習的 ... 於 books.google.com.tw -
#50.博润伟业-SQE-供应商质量管理高级研修班
本课程的目的,是通过系统化的介绍,让学员了解: 1、实际了解质量管理原则在采购产品的整个寿命周期中的应用; 2、理解供应商质量 ... 於 www.brwy.com -
#51.“供应商品质管理(SQE)实战训练”培训课程方案提供 - 博猫2游戏
【博猫2游戏】如果贵公司有“供应商品质管理(SQE)实战训练”或类似培训需求,请填写下表信息,我们将根据贵公司的实际培训需求,提供符合贵公司要求的课程培训方案. 於 www.aoweiad.com -
#52.SQE-供应商质量管理与实务 - 企赢培训学院
企赢培训学院为你提供徐志坚老师供应商管理培训课程《SQE-供应商质量管理与实务》,想了解更多《SQE-供应商质量管理与实务》课程相关信息,请咨询:18820199226. 於 www.qiyingschool.com -
#53.SQE供应商质量管理培训课程_叶礼平讲师
SQE 供应商质量管理培训课程课程背景在今日企业的生产活动中,强调供应链一体化,外购、外协部品在生产成本中所占的比例往往占到总成本的一半以上或更高。 於 m.nlypx.com -
#54.Youtube上2CExam很多人浏览的EAQE/SQE影片课程现在还 ...
2CExam近年推出了一系列EAQE(地产代理资格考试,地产大牌考试)及SQE(地产代理营业员资格考试,地产细牌考试)的线上影片课程,课程整合了整份考卷 ... 於 2cexam.com.hk -
#55.科學人(第169期/2016年3月號): SM169 - 第 95 頁 - Google 圖書結果
超越學校課程的突破性研究報導,提供與全球科學家同步思考的前瞻性思惟, ... 圓形和新月形的符號象徵了太陽及新月,而小形圓點則代表了恆星和行星。其中. SQE \團* 於 books.google.com.tw -
#56.SQE供應商質量管理及工具運用李兆山 - 看看文庫
培訓物件:sqe、品質工程師、iqc來料檢驗經理、採購經理、**商輔導專案經理、研發經理、市場經理等。 課程背景:. 近年來我們聽到越來越多的因產品 ... 於 www.ikanpan.com -
#57.讓有志成為律師的人士透過全新路徑,獲取英格蘭和威爾斯的 ...
SQE 的推行最終將會令法律深造文憑(Graduate Diploma in Law - GDL)和法律實務課程(Legal Practice Course - LPC)在英格蘭和威爾斯內停辦。這條獲取 ... 於 hk-lawyer.org -
#58.110-1 林口長庚醫院報到相關注意事項
閱讀COVID-19影片須完成課程訓練名冊(如附加檔案)。 2.SQE已建檔~ 請於實習當天開始須上本院院外之員工專區登入每天體溫(如非受雇人員帳號申請作業流程說明(師生版))。 於 www.nursing.fju.edu.tw -
#59.新概念英语青少版入门级A Unit 11 原声音频+课文动画视频+ ...
... 新概念英语”教学体系的成员,是专为中国的青少年以及英语初学者编写的。考虑到了中国国家课程标准对中、小学生的知识能力的要求,所以全套教材内容. 於 sunnews.cc -
#60.广州SQE供应商管理公开课-胶东在线考试培训
诺达名师的供应商质量管理课程,向学员讲解丰富的采购中的质量问题,包括了采购和质量的战略分析,供应商全面质量管理,采购质量检验和质量控制技术等 ... 於 www.jiaodong.net -
#61.電子料SQE培訓計劃
本資訊是關於SQE的培訓課程有哪些,做SQE都需要掌握哪些基礎知識,SQE年度重點工作計劃, ... SQE(Supplier quality engineer)供應商質量工程師 於 www.tui18edu.com -
#62.SQE - MBA智库百科
SQE (supplier Quality Engineer,供應商質量工程師)SQE是供應商質量工程師的簡稱,是質量管理細分後的一個 ... 做SQE,現有產品的質量保障工作是基本功,也是入門課程。 於 wiki.mbalib.com -
#63.SQM供應商管理與輔導- 課程資訊
課程 大綱: 一、供應商管理之重要性 二、公司規模與供應商類型 三、供應商輔導 -SQE輔導能力培養 -日常管理 -各種執行面之輔導方式:進料驗收、異常處理、專案輔導 ... 於 edu.cpc.org.tw -
#64.SQE:供应商质量管理及工具运用_内训课程 - 天天直播安卓 ...
为此我们结合多家知名跨国公司的运作管理模式,结合本身咨询师的工作经验以及最新的物料品质和供应链管理知识,专门开发了这一个面向制造业SQE的专项课程。 於 huayuliu.com -
#65.SQE—供应商质量管理 - 关于多彩
SQE —供应商质量管理企业培训课程是行课网提供采购物流类培训龚举成讲师主讲的课程,SQE—供应商质量管理企业培训课程属于采购物流领域企业培训课程。企业管理培训公司行 ... 於 www.ystrade.net -
#66.實習組成員 - 護理系- 長庚科技大學
6.辦理教師急救訓練課程及實習師生SQE資料建置。 7.辦理實習指導教師考勤等相關業務。 8. 於 ns.cgust.edu.tw -
#67.標籤: 采購經理 - 亚诺培訓教育網
適合對象· 采購經理· SQE 課程安排2021-08-27北京2022-01-07北京培訓講師:王大勇 課程價格:¥5400元/人 培訓天數:3天 課程大綱供應管理培訓培訓對象:采購主管及 ... 於 train.yn59w.cn -
#68.英國升學講座「法律課程如何助您事業發展?」
現有的法律實務課程(LPC) 將會被2021年9月推出的Solicitors Qualifying Examinations(SQE)逐步取代,如果想沿用現有LPC途徑成為英國事務律師又尚未持有法律學位的 ... 於 www.hkosc.com.hk -
#69.SQE品保|在職進修|線上學習|104求職精靈
求職精靈提供豐富的「SQE品保」學習資源,您可以在此觀課教學與文章,並進行測驗,管理自我學習成長歷程。 ... 【地政士專業科目考前衝刺課程_影音函授】05. 於 nabi.104.com.tw -
#70.供应商质量管理(SQE)
供应商质量管理(SQE)(12月13日深圳班),本次课程重点,在信息日益发达与透明的今天,企业间竞争已成为整个供应链的竞争,对于供应商而言无不接受到来自品质、成本、 ... 於 www.dulcecake.com -
#71.SQE(律师资格考试) - 4manbet .cc
准备SQE. SQE Prep. 有许多选项对于如何为SQE准备,从专业课程到 ... 於 www.georgeputman.com -
#72.Alan Hsu - SQE - NVIDIA | LinkedIn
Alan Hsu. NVIDIA SQE. NVIDIANational Tsing Hua University. 台灣Taiwan Hsinchu City500+ 位聯絡人. 於 tw.linkedin.com -
#73.最牛崗位SQE供應商質量工程師實戰培訓講義及供應商管理方法 ...
做SQE,現有產品的質量保障工作是基本功,也是入門課程。通過對實際問題的處理,對各種失效模式和失效後果親身的體會和認識,達到專業積累的增加和經驗 ... 於 kknews.cc -
#74.品質管理教育訓練課程系列 - 佳威企管
雖然企業有品管部門與品保部門,但是對於品管訓練,品管課程,品管講師,品管顧問了解 ... 管理工程師(SQE)、製程品質管理工程師(PQE)、實驗室人員、客訴處理工程師(CSE). 於 www.goodway-mcc.com.tw -
#75.營業員資格考試SQE 課程(細牌)(S牌)講解[不是Past ... - YouTube
本影片不是Past Paper, 不是Pass Paper, 不能Download, 不能下載,沒有PDF主要講述營業員資格考試SQE (細牌)(S牌)課程內容,如同學如需購買模擬試題 ... 於 www.youtube.com -
#76.SQE,供应商质量管理广州课程 - 北京大学总裁班
【参加对象】SQE,品质工程师/经理、IQC来料检验主管、体系工程师/ ... 住宿统一安排,费用自理;【课程背景】企业间竞争已成为整个供应链的竞争是 ... 於 bdzgzx.com -
#77.英国执照最新考试SQE 线上课程视听介绍! - 健康心得
Peter 2000年开始就职于法学大学,教授GDL, MA Law, LPC,主导参与ULAW新SQE路径下的课程设计,包括PGDL, MA Law (Conversion), MA Law(SQE1) ... 於 www.anmoyi98.com -
#78.法律专业资格的重要变更:有抱负的律师的信息
我们目前正在改变LLB法律课程,以确保我们的学生准备介绍SQE途径资格。 专业资格有哪些变化? 目前,成为英格兰和威尔士的律师有三个阶段:. 学术阶段(资格法律学位) ... 於 www.meremoggies.com -
#79.《SQE-供应商质量管理高级研修班》-教育频道 - 手机搜狐
课程 对象:SQE,品质工程师/经理、IQC来料检验主管、体系工程师/主管、采购工程师/经理、供应商辅导项目工程师/经理、研发经理、市场经理等。 【课程主办】深圳市华晟 ... 於 m.sohu.com -
#80.訓練課程:非品質主管應具備的品質素養課程日期 - 易騰企管首頁
課程 大綱: 1、公司組織與品保組織的關係 2、質與量的博弈 3、誰是我們的客戶 4、品質系統在做什麼 5、研發與品質部門的互動 6、SQE/IQC的關係 7、PQC製程品管要做什麼 於 www.etbest.com.tw -
#81.SQE Courses: Prepare for the SQE
Find out everything you need to know about the SQE and the courses that will help you prepare for the Solicitors Qualifying Exam. 於 www.solicitor-exams.co.uk -
#82.供应商质量管理SQE培训- 公开课
供应商质量管理SQE. 课程编号:4511[ 加入收藏 ]. 时间地点Location/Date:2021-12-24 至2021-12-25 广州; 授课讲师Lecturer:刘老师; 费用Fee:4580元/位(获赠学习 ... 於 cpoway.com -
#83.SQE供应商质量管理SQM/供应商质量工程师SQE培训
课程 名称: S.Q.E供应商质量管理SQM/供应商质量工程师SQE培训; 课程编号: SQE_Hay; 课程课时: 2天; 培训费用: 8,800.00RMB/人; 其他备注: 世界500强外企资深质量 ... 於 www.haythink.com -
#84.成都SQE供应商质量管理高级研修班学费_其它培训价格_成都方普 ...
成都方普培训网站免费提供成都其它培训价格,成都SQE供应商质量管理高级研修班学费 ... 課程介紹. 為何選擇方普管理? 方普管理是國內認證、咨詢、培訓一體化標準服務 ... 於 www.gmcnutrition.com -
#85.SQE:供应商质量管理及工具运用
【课程简介】 物料质量和供应商管理在不同的企业中的应用,使SQE(Supplier Quality Engineering)的职位应运而生。事实上,供应商品质管理的内容非常 ... 於 cips-china.com -
#86.SQE培训课程【汇名家网】
汇名家网为您提供SQE培训(SQE培训,SQE培训课程)丰富的资源,包括SQE培训方案、SQE培训计划、SQE培训课件、SQE培训课程、SQE培训讲师、SQE培训公司、SQE学、SQE培训 ... 於 www.huimingjia.com -
#87.培训邀请| SQE或者想做SQE的速来报道!!! - 手机搜狐网
课程 收益. 了解供应商质量工程师(SQE)岗位背景、职责、能力模型及职业发展路径;. 掌握供应商质量工程师(SQE)在产品开发、供应商管理、改善等流程 ... 於 www.sohu.com -
#88.SQE – Become an English Solicitor - Google Play 應用程式
QLTS School offers preparation courses for the Solicitors Qualifying Examination (SQE), the centralised assessment to qualify as a solicitor ... 於 play.google.com -
#89.供应链质量管理(SQE)培训-STG百胜技术— 做认证
本课程,关注供应商质量管理中的核心工作模块以及能力发展需要,并希望借助这个课程平台,为SQE同仁搭建一个沟通交流的平台,帮助大家在此领域获得启发,取得长足的 ... 於 www.bsrenzheng.com -
#90.顧問技能和養成實作 - 第 249 頁 - Google 圖書結果
A.類數位學習課程..播放 1 次課程主題之時數方式. ... 供應商品質工程 14 小時翁田山(品保+驗收+採購+SQE)工程師及主管大綱參考附件 10 實體授課課程說明: A.以上共 10 ... 於 books.google.com.tw -
#91.SQE 即供應商質量工程師(Supplier Quality Engineer)。職
SQE 即供應商質量工程師(Supplier Quality Engineer)。職責:1、負責保障供應商所供原材料的質量,由于供應商供貨物料質量缺陷引發的問題要及時反饋供應商要求其改善 ... 於 www.itsfun.com.tw -
#92.開課課程內容
供應商品質工程(SQE) ... 為尊重講師之智慧財產權,恕無提供課程講義電子檔。 ... 管理角度的思維4.1採購總成本觀4.2SQE所有資源活動也是成本4.3微利時代的品質觀念4.4 ... 於 www.topchina.com.tw -
#93.2016/3/18: ISO 9001:2015 高階主管課程(新竹場) - 優麗國際 ...
課程 大綱:用「人性化的策略領導與管理」角度來闡述ISO 9001:2015 ... (因為内稽人員也必需有能力稽核第4、5 和6三個章節)、供應商稽核員/SQE (供應商 ... 於 www.dqs.tw -
#94.返工(重工)和返修的区别~择宽企管QA、QC、SQE、QE
返工(重工)和返修的区别~择宽企管QA、QC、SQE、QE、PQE、质量管理、品质 ... 如果质量朋友们希望线上学习ISO内审员课程,获得ISO内审员证书,可以 ... 於 www.bilibili.com -
#95.比较13 个法律实践硕士学位
University of Law SQE. 伦敦, 英国+10 更多 ... 该课程是为希望获得律师资格并获得硕士水平的法律资格的非法学毕业生而设计的。作为国际认可的资格,法律硕士是您投资 ... 於 www.masters-abroad.com -
#96.【考取英國事務律師資格新制度及課程(SQE) 】升學講座 - Stay ...
考取英國事務律師資格新制度及課程(SQE) 】升學講座at 香港教育資訊網, 軒尼詩道48-62 號上海實業大廈901室, Hong Kong, Hong Kong on Mon Apr 26 ... 於 stayhappening.com -
#97.台大醫院- 基本生命復甦術(BLS)課程
位置: 總院-2013基本生命復甦術(BLS)課程> 測驗(104年基本生命復甦術(BLS)測驗) 有效期間: 2014-12-15 00:0. ... 屬性, 內訓課程/ 線上課程. 類別, (SQE)急救訓練. 於 thermage.pixnet.net